The 4-Minute Rule for Lean Manufacturings
Wiki Article
The Facts About Hon Hai Precision Revealed
Table of ContentsMore About Additive ManufacturingThe smart Trick of Plastic Manufacturing That Nobody is DiscussingGet This Report on Plastic ManufacturingUnknown Facts About Additive Manufacturing
With shot moulding, pre-dried granular plastic is fed by a forced ram from a receptacle into a warmed barrel. As the granules are gradually relocated forward by a screw-type plunger, the plastic is pushed into a heated chamber, where it is melted. As the bettor advancements, the melted plastic is forced with a nozzle that relaxes against the mould, enabling it to go into the mould dental caries via a gateway and also jogger system.The series of occasions during the shot mould of a plastic component is called the injection moulding cycle. The cycle begins when the mould shuts, adhered to by the shot of the polymer into the mould cavity. Once the dental caries is loaded, a holding pressure is kept to make up for product shrinking.
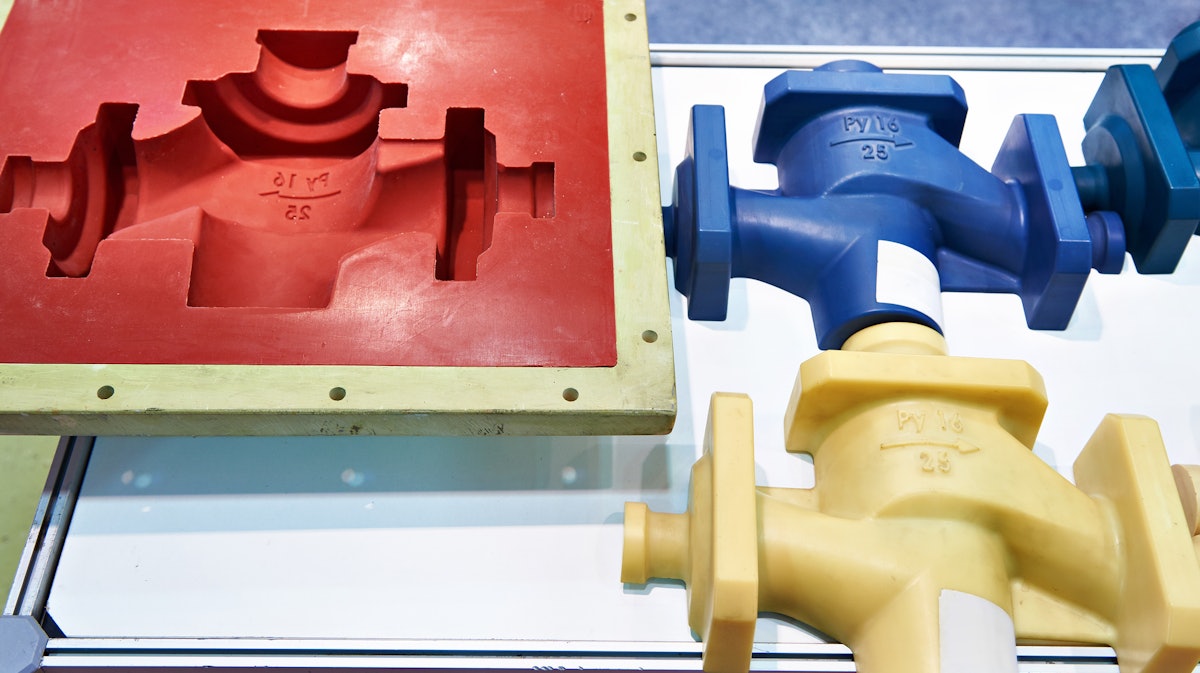
Once the dental caries is 98% complete, the equipment switches over from velocity control to stress control, where the cavity is "loaded out" at a consistent stress, where adequate velocity to reach wanted stress is needed. This allows employees control component measurements to within thousandths of an inch or far better. Like all commercial processes, shot molding can generate problematic parts, even in playthings.
Examine This Report about Manufacturing
Trials are usually done prior to complete manufacturing runs in an effort to predict flaws and also establish the suitable specs to make use of in the shot process.: 180 When loading a new or unfamiliar mould for the very first time, where shot size for that mould is unidentified, a technician/tool setter might perform a trial run before a full production run.
Holding stress is enhanced till the parts are complimentary of sinks and component weight has been attained. Injection moulding is an intricate innovation with possible production troubles. They can be triggered either by issues in the moulds, or a lot more often by the moulding procedure itself.: 4785 Moulding defects Different name Summaries Causes Blister Blistering Elevated or layered area on surface of the part Device or material is also hot, often triggered by a lack of cooling around the device or a faulty heating unit.
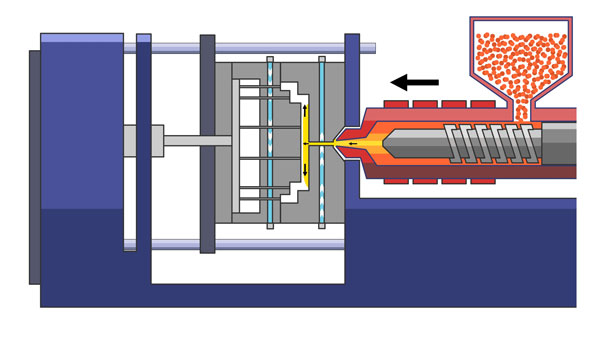
Facts About Plastic Manufacturing Revealed
Embedded particulates Foreign particle (burnt product or other) ingrained in the part Particles on the device surface, contaminated material or international debris in the barrel, or way too much shear warm burning the product before injection. Flow lines Directionally "off tone" wavy lines or patterns Shot speeds also sluggish (the plastic has actually cooled off also much throughout injection, injection rates should be established as fast as is ideal for the procedure as well as product used).Filling up as well fast, not enabling the sides of the part to set up. Mould may be out of enrollment (when the 2 halves don't centre appropriately and part wall surfaces are not the exact same density). The offered info is the usual understanding, Adjustment: The Absence home of pack (not holding) stress (pack pressure is used to pack out although is the component during the holding time).
In other words, as the part reduces the material divided from itself as there was not sufficient resin in the tooth cavity. The gap can take place at any area or the component is not restricted by the density however by the material circulation and also thermal conductivity, but it is most likely to occur at thicker locations like ribs or managers.
Knit line/ Blend line/ Transfer line Discoloured line where two flow fronts meet Mould or material temperature levels set too low (the material is cold when they meet, so they don't bond). Time for shift between shot and also transfer (to packaging as well as holding) is prematurely. Turning Altered part Cooling is too short, material is too warm, absence of cooling around the device, wrong water temperature levels (the components bow inwards in the direction of the warm side of the tool) Uneven shrinking between locations of the component.
The Oem Ideas
125 inch wall density is +/- 0. 008 inch (0. 2 mm).: 446 Power demands [modify] The power required for this process of shot moulding depends upon many things and also jabil healthcare ranges products used. Production Processes Referral Guide mentions that the power requirements depend upon "a product's particular gravity, melting factor, thermal conductivity, component size, as well as molding price." Below is a table from page 243 of the exact same referral as formerly discussed that ideal illustrates the attributes pertinent to the power needed for the most typically utilized materials.In addition to installing assessment systems on automated tools, multiple-axis robots can eliminate parts from the mould as well as position them for additional processes. Details circumstances consist of eliminating of components from the mould immediately after the parts are produced, in addition to applying device vision co packer systems. A robot holds the part after the ejector pins have been extended to free the component from the mould.
Why is shot molding maker manufacturing so effective? And exactly how does it function? To learn, let's dig right into the subject and answer every one of the crucial concerns, including what it is, the process behind it, its main advantages, and also exactly how to select the ideal provider. What is Shot Molding? is the process of making use of plastic to manufacture a large range of parts and products.
The injection molding maker utilizes personalized mold and mildews to fill them out according to requirements, creating identical duplicates that can be personalized in a variety of methods. What's more, shot molding is an extremely versatile process, allowing for a variety of different products as well as surfaces, that makes it a popular alternative in numerous industries with entirely different objectives and also requirements - lean manufacturing.
Report this wiki page